Boeing Open-Hole Compression Test Fixture (ASTM D6484)
Model No. WTF-OH (Stainless Steel)
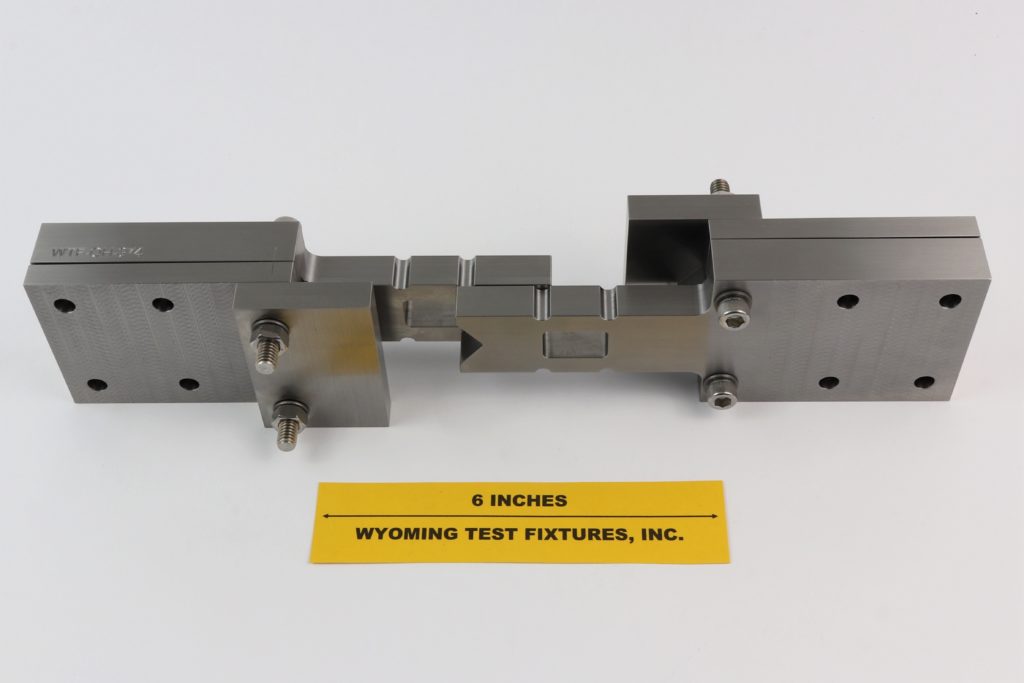
Fig. 1: Assembled Fixture without specimen installed.
The Boeing Open-Hole Compression Test Fixture was developed by the Boeing Company (Reference 1 thru 4). The general test method is also described in SACMA Recommended Method SRM 3R-94 (Reference 2). The latest Boeing version of the fixture, described in References 3 and 4, has been adopted as ASTM Standard D6484 (Reference 5).
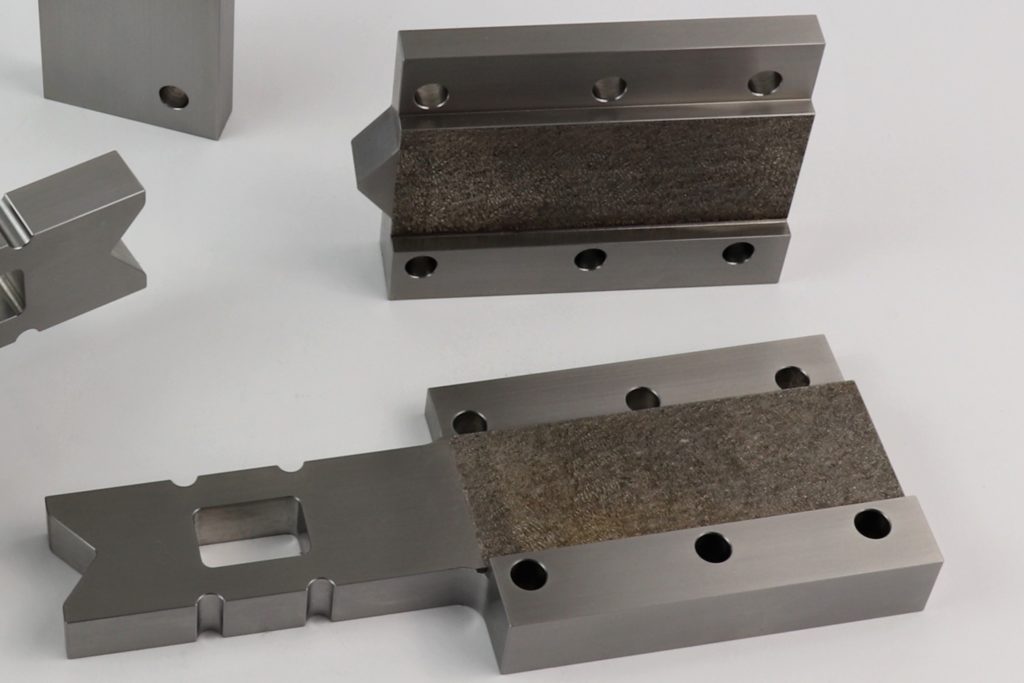
Fig 2: Disassembled fixture, showing the thermal-sprayed gripping surfaces
The specimen, typically, but not necessarily, a quasi-isotropic laminate, is 12" long, 1.5" wide, and approximately 0.1" thick, and contains a 0.25" diameter hole in its center. A NASA standard, described in Reference 6, specifies a much wider (5" wide) specimen and thus is not commonly used, being less conservative of the material being tested. A much more popular competitor to the Boeing configuration is the Northrop Open-Hole Compression Test Fixture (Reference 7), Wyoming Test Fixtures Model WTF-NH. A detailed comparison of these fixtures is presented in Reference 8. Additional discussion can be found in Reference 9.
The Boeing Open-Hole Compression test specimen is shear- or end-loaded in compression to failure in the fixture shown in Figs. 1 and 2, the specimen extending from one end to the other of the fixture. The fixture supports the test specimen continuously along both faces, a sufficient gap being designed into the staggered v-shaped joints in both sides of the fixture (see the partially assembled fixture in Fig. 2) so that no contact occurs across these joints during the compressive loading of the specimen. Guide plates are provided on each side of the fixture to maintain alignment of the assembly.
The assembled fixture, with specimen installed, can be gripped at each end by hydraulic grips in the testing machine (shear loading), or aligned vertically between flat platens (end loading). Shear loading is preferred in the Boeing specification, but requires relatively large hydraulic grips, i.e., typically at least 2" wide and capable of opening at least 1.3", as indicated in Fig 3.
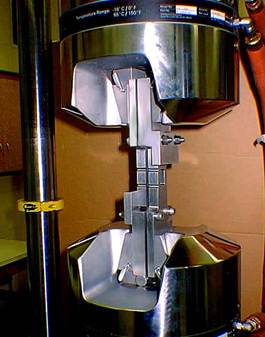
Fig. 3 Boeing Open-Hole Compression Test Fixture clamped in 55 kip hydraulic grips
If the specimen is end-loaded, it may be desirable to provide some additional clamping force at the ends of the specimen, to minimize end-brooming. ASTM D6484 (Reference 5), in the 2004 revision, added four holes in each end of the fixture for clamping bolts, as shown in Fig 4. These holes are now incorporated in the Model WTF-OH fixture.
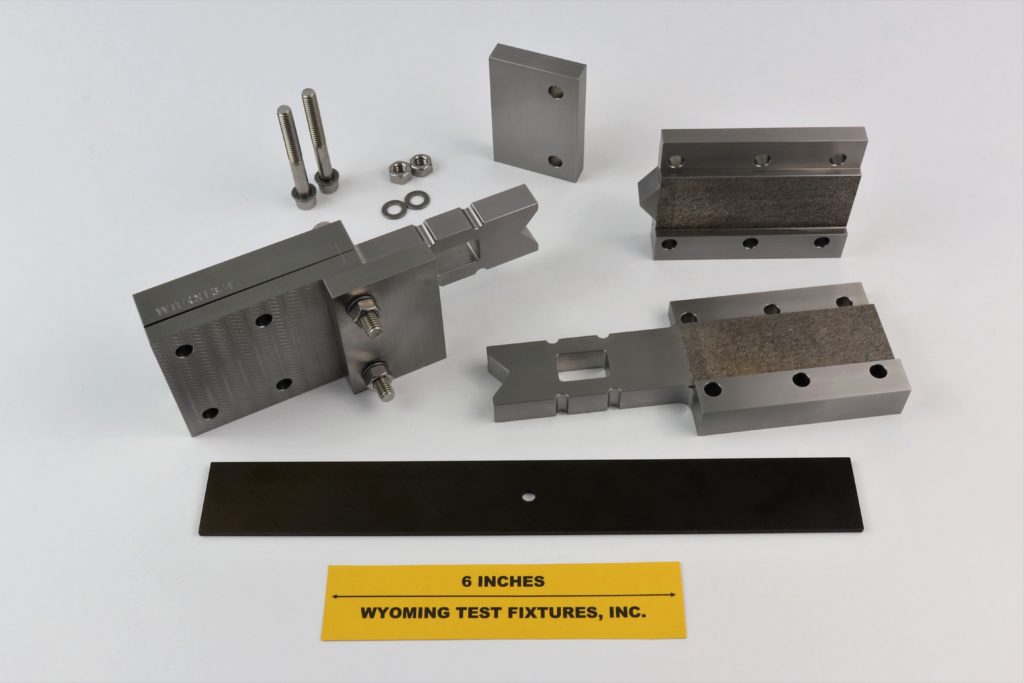
Fig 4. ASTM D6484-04 (2004) version of fixture with four additional bolt holes at each end, for mechanical clamping of specimen if end-loaded.
If the fixture is loaded between flat platens, some type of lateral constraint should be provided so that the fixture does not slip out from between the platens while being compression loaded, as a safety precaution. Slipping the ends of the fixture into shallow box-like fittings attached to the testing machine is one such option available from Wyoming Test Fixtures, Inc., as shown in Fig 5.
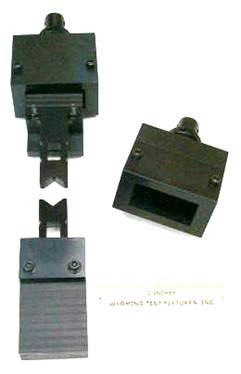
Fig 5. End constraint boxes for use when end-loading the specimen.
An early version of the Boeing Open-Hole Compression Test Fixture included cutouts to clear strain gages bonded to the surfaces of the specimen, and to provide egress for the gage wiring. This fixture is shown in Fig 6. Subsequent Boeing specifications, and the ASTM standard, do not include these cutouts, strain gages not being used.
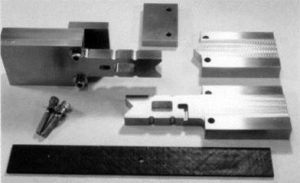
Fig 6. Boeing BSS 7260 version of open-hole compression test fixture, with cut-outs added for strain gages, threaded alignment plates, and machine-roughened gripping surfaces. A standard 12" by 1.5" wide test specimen with a 0.25" diameter central hole is shown at the bottom.
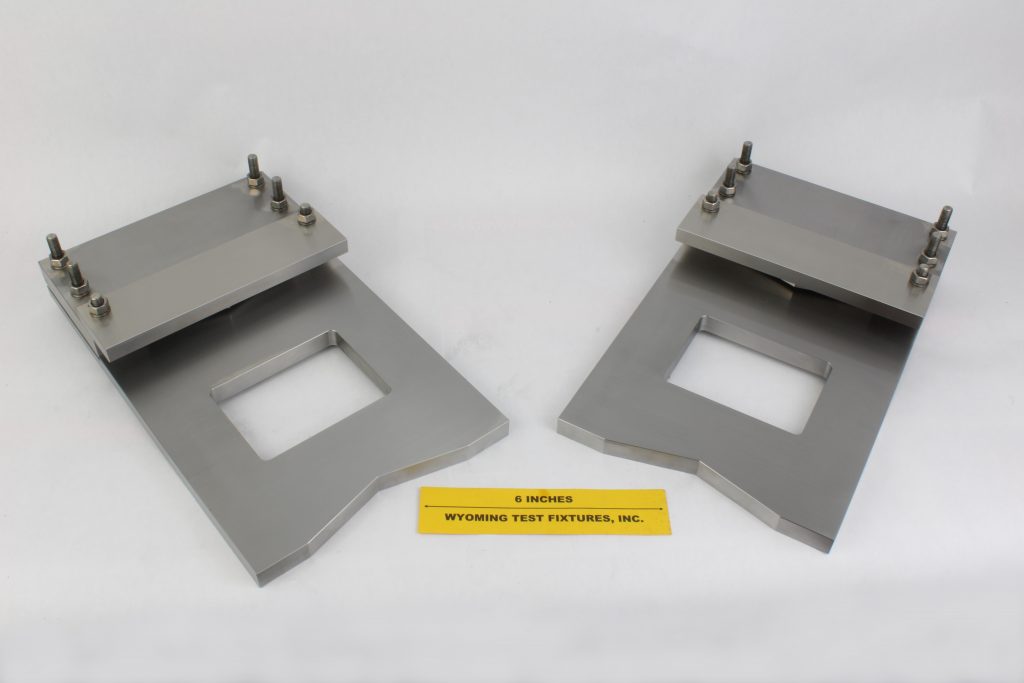
Fig. 7: Custom Boeing Open Hole Compression Test Fixture for 6 x 17" specimens
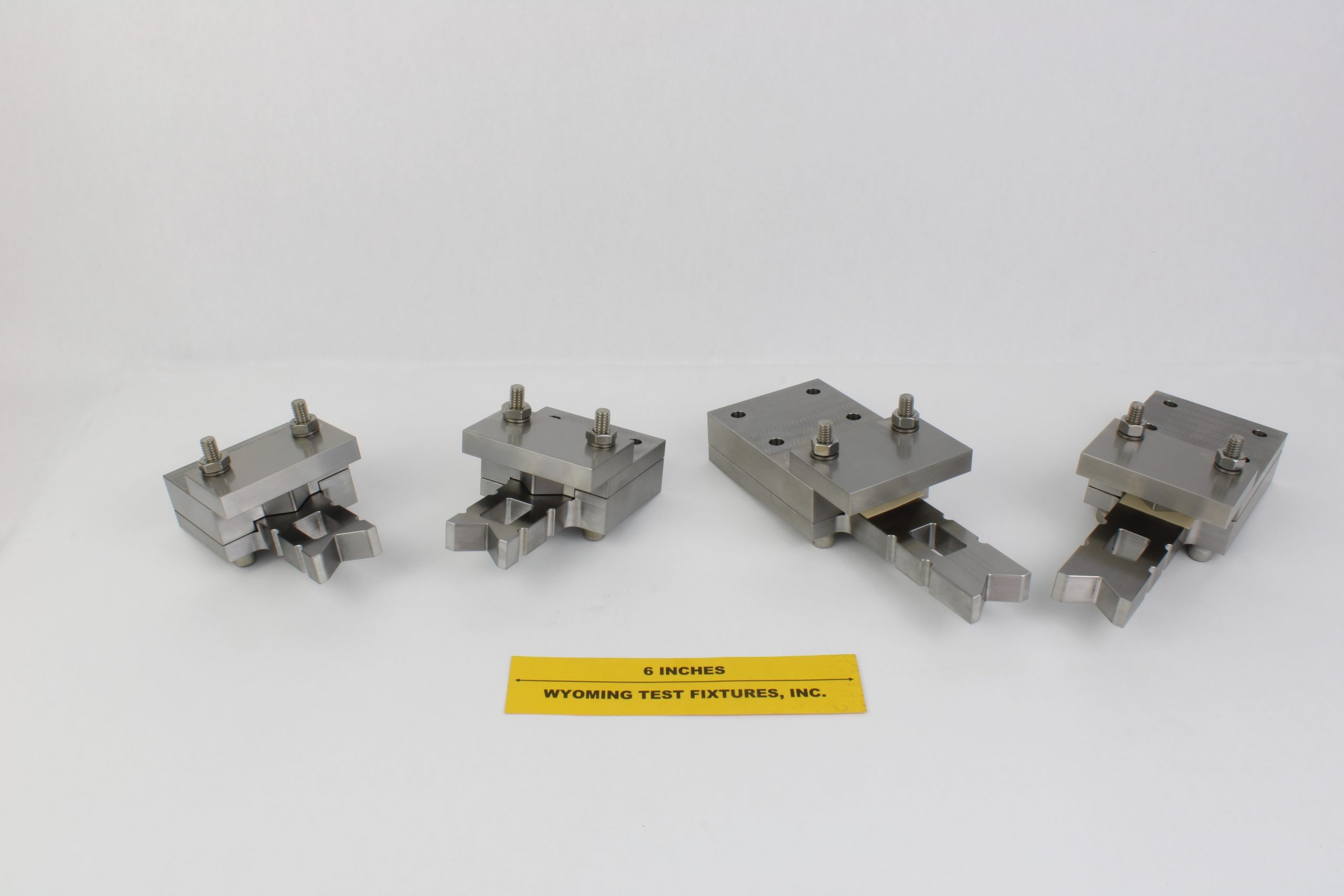
Fig. 8: Custom Small Boeing Open Hole Compression Test Fixture (for 1.5 x 7.5" specimens) is shown on the left with a standard fixture shown on the right.
Sources of Additional Information:
1) Boeing Specification Support Standard BSS 7260, "Advanced Composite Compression Tests," The Boeing Company, Seattle, Washington (originally issued February 1982, revised December 1988).
2) SACMA Recommended Method SRM 3R-94, "Open-Hole Compression Properties of Oriented Fiber-Resin Composites," Suppliers of Advanced Composite Materials Association, Arlington, Virginia, 1994.
3) Boeing Document No. D888-10026, "Test Methods for Advanced Composites," The Boeing Company, Seattle, Washington, January 1996.
4) Boeing Document No. D6-83079-71, “Test Method for Compressive Properties of Thin Composite Lamina and Laminates,” The Boeing Company, Seattle, Washington, November 2003.
5) ASTM Standard D6484/6484M-09 (2009), "Open-Hole Compressive Strength of Polymer Matrix Composite Laminates," American Society for Testing and Materials, West Conshohocken, Pennsylvania (first issued in 1999).
6) NASA Reference Publication 1092, "Standard Tests for Toughened Resin Composites," NASA-Langley Research Center, Hampton, Virginia, Revised Edition, July 1983.
7) Northrop Specification NAI-1504C, "Open Hole Compression Test Method," Northrop Corporation, Hawthorne, California, May 1988.
8) S.L. Coguill and D.F. Adams, "A Comparison of Open-Hole Compression Fixtures by Experimental Evaluation," Proceedings of the 45th International SAMPE Symposium and Exhibition, May 2000.
9) D.F. Adams, “Open Hole Compression Testing,” High Performance Composites, March 2005, pp. 12-13.